Quality standards in construction are a cornerstone of modern building projects, serving as benchmarks to ensure safety, efficiency, and compliance. These standards guide the industry, offering frameworks that help projects meet their intended goals while satisfying regulatory and client expectations. For companies focused on design, consultation, and supervision, adhering to these standards is essential to delivering projects that align with approved designs, budgets, and timelines.
Construction quality control involves structured management practices to ensure project deliverables meet established guidelines.
This encompasses two primary aspects:
- Quality Assurance: Establishing the policies and procedures that define expectations for project outcomes.
- Quality Control: Implementing specific plans and checks to achieve those outcomes consistently.
By aligning these processes, construction professionals can identify and address issues early, prevent recurring problems, and deliver high-quality results. As the construction industry plays a pivotal role in the economy, maintaining quality standards is vital for sustaining trust and reliability.
What Are Quality Standards in Construction?
Quality standards in construction are established frameworks and codes that govern the planning, design, and supervision of building projects. These standards, such as ASTM International, ISO 9001, and LEED certifications, ensure projects adhere to high benchmarks for safety, sustainability, and efficiency.
- ASTM (American Society for Testing and Materials): Provides technical standards for materials, products, and systems used in construction.
- ISO 9001: Focuses on quality management systems, ensuring consistent project quality and customer satisfaction.
- LEED (Leadership in Energy and Environmental Design): Promotes sustainability by certifying environmentally friendly building practices.
By adhering to these standards, construction consultants ensure their designs and supervision processes comply with stringent guidelines, minimizing risks and enhancing overall project outcomes.
Why Are Quality Standards Important?
Quality standards in construction have a direct impact on project success, benefiting all stakeholders involved.
Benefits for Clients
- Peace of Mind: Clients gain confidence that their projects will meet safety and quality benchmarks.
- Cost Efficiency: Avoiding delays and costly rework saves significant resources.
- Longevity: High-quality construction ensures durability and reduces long-term maintenance costs.
Benefits for Consultants
- Professional Credibility: Adhering to recognized standards enhances reputation and trust.
- Regulatory Compliance: Following standards like ISO 14001 ensures alignment with environmental and safety regulations.
- Streamlined Processes: Standards provide a clear framework for managing projects effectively.
Benefits for the Public
- Safety: Projects meeting quality standards reduce hazards and ensure public well-being.
- Sustainability: Standards like ISO 50001 promote energy efficiency and environmental stewardship.
By prioritizing quality standards, consultants and clients alike contribute to safer, more reliable infrastructure.
Common Quality Control Measures
Ensuring compliance with quality standards in construction involves systematic processes, including:
Inspections
Frequent on-site inspections during the design and supervision phases help identify discrepancies early, ensuring adherence to approved plans.
Testing
Material testing ensures all components meet specified requirements, from strength to durability. This is crucial in design to ensure structures can bear intended loads.
Audits
Regular audits of procedures and documentation help maintain consistency and transparency throughout the project lifecycle.
Together, these measures create a comprehensive approach to maintaining quality standards, aligning with client expectations and industry requirements.
Challenges in Maintaining Quality Standards
Despite their importance, maintaining quality standards in construction can be challenging.
Common Challenges
- Inadequate Documentation: Poor record-keeping can lead to missed details and non-compliance.
- Limited Awareness: Some stakeholders may lack knowledge of the latest standards and codes.
- Budget Constraints: Tight budgets can pressure teams to compromise on quality.
Overcoming These Challenges
- Training: Regularly educate teams on updates to industry standards.
- Technology Adoption: Utilize advanced tools like Building Information Modeling (BIM) for better oversight.
- Efficient Resource Management: Focus on cost-effective strategies that do not compromise quality.
The Future of Quality Standards in Construction
Emerging technologies and trends are set to revolutionize quality control in construction:
Automation and AI
- AI-driven tools can analyze project data to predict and prevent potential quality issues.
- Automated inspection systems enhance accuracy and reduce human error.
Sustainability Standards
- Green building practices, like those outlined in LEED certifications, are becoming more prevalent.
- Companies adopting ISO 50001 standards showcase leadership in energy efficiency.
Digital Twin Technology
This innovation allows teams to create virtual models of projects, enabling real-time monitoring and quality control.
Kayan's Comprehensive Supervision System: Ensuring Quality Standards in Construction
At Kayan Engineering Consultancy, maintaining quality standards is achieved through a robust four-level supervision system that ensures precision, efficiency, and compliance across all phases of construction. This system integrates direct supervision by engineers through regular site visits, weekly evaluations by a support team, monthly project manager assessments, and bi-monthly branch manager oversight. This layered approach facilitates seamless communication among stakeholders, early detection of potential issues, and adherence to approved designs, timelines, and budgets. By aligning with established standards such as ISO and LEED, Kayan ensures the integration of sustainable practices, advanced technologies, and meticulous quality control. This commitment to excellence not only enhances project outcomes but also reinforces Kayan’s reputation as a leader in delivering safe, efficient, and environmentally responsible construction solutions.
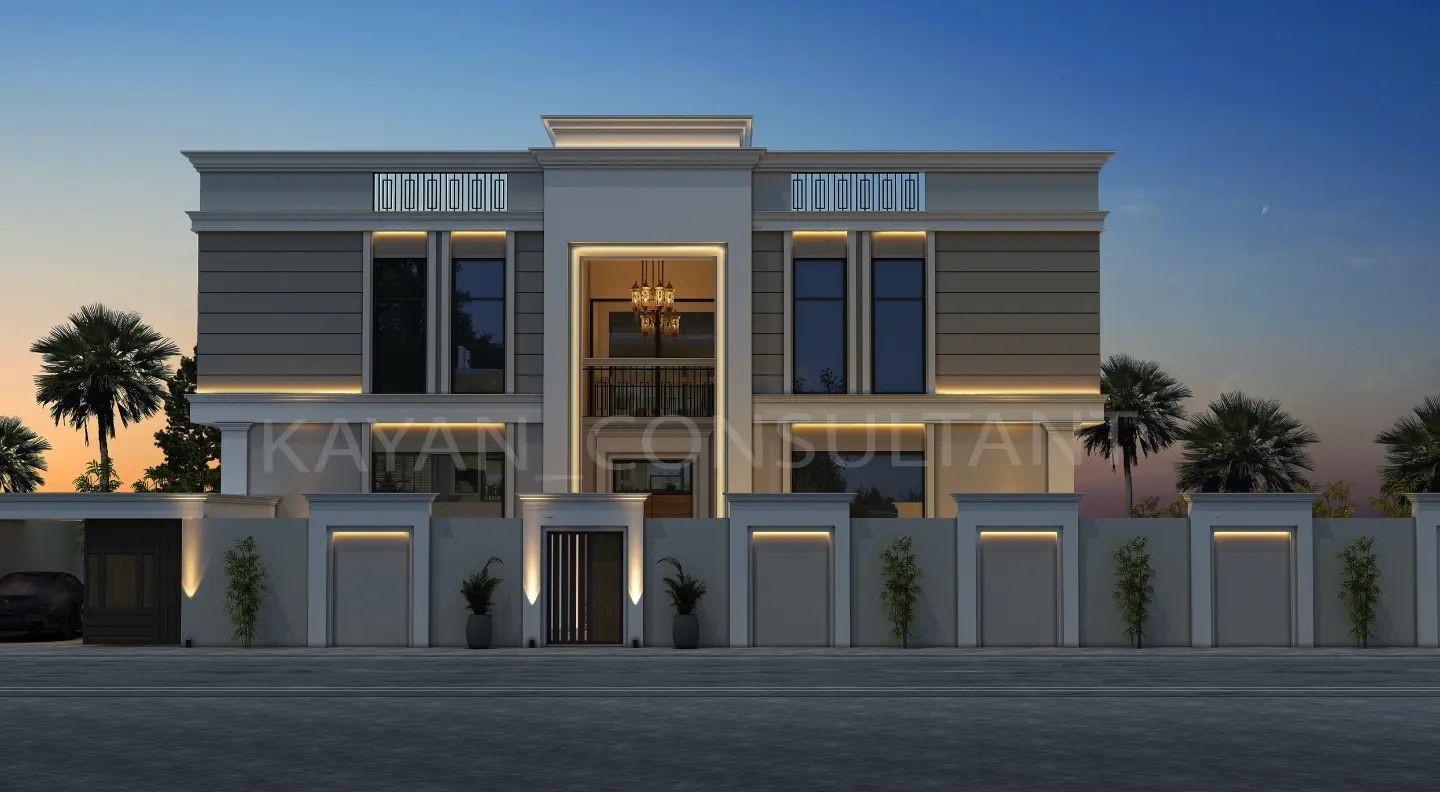
- Kayan Engineering Consultants is the best engineering consulting office in the UAE.
Conclusion
Quality standards in construction are essential for ensuring project success, safeguarding public safety, and fostering sustainable practices. By adhering to established frameworks like ASTM, ISO, and LEED, consultants can deliver projects that meet the highest benchmarks for safety, efficiency, and environmental responsibility.
Frequently Asked Questions
What are quality standards in construction?
Quality standards are established benchmarks that ensure projects meet safety, efficiency, and sustainability requirements.
How do quality standards benefit clients?
They ensure projects are completed on time, within budget, and to a high standard, reducing long-term costs and risks.
What challenges arise in maintaining quality standards?
Common challenges include inadequate documentation, limited awareness of standards, and budget constraints.
How is technology influencing quality standards?
Technologies like AI, automation, and digital twin models are streamlining quality control processes and improving project outcomes.
What role does Kayan play in promoting quality standards?
Kayan Engineering Consultancy ensures adherence to the highest quality benchmarks, providing exceptional design, consultation, and supervision services.